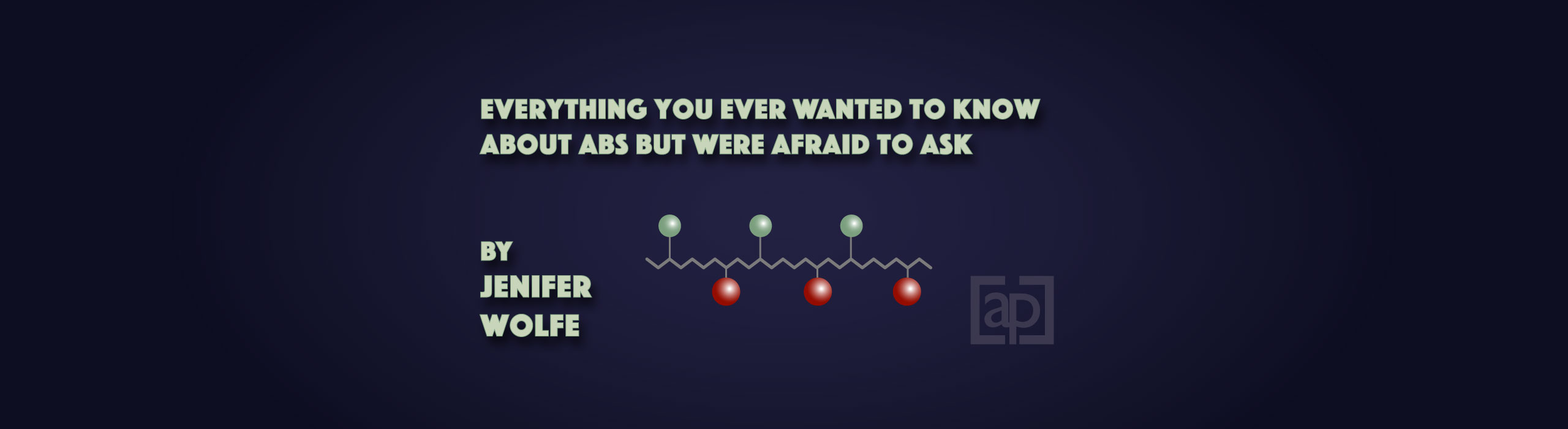
Plastic Types: ABS Plastic
How ABS Plastic Clawed Its Way to World Domination
Worlds have been built with ABS plastic. As the material for most LEGO bricks and accessories, ABS is perhaps the most common “building” material in the known universe. The company’s splashy announcement in 2015 that it would search for a non-oil-based plastic to replace ABS came with a rather large but: they don’t expect said replacement to be complete until 2030, and the initiative will cost $150 million. Which is to say, ABS will be hard to replace for the notoriously finicky LEGO. What is this magical substance and what makes it nearly irreplaceable? Let’s find out.
The ABCs of acrylonitrile butadiene styrene
Those three polymers are the building blocks of the ABS plastics family. Acrylonitrile is produced industrially by the process of ammoxidation, which involves forcing ammonia and oxygen through a reactor with another gas or liquid, in this case propylene, to create a nitrile. Acrylonitrile does not occur naturally in Earth’s atmosphere, but interestingly it has been detected around Titan, one of Saturn’s moons, so maybe we’ll see interlocking brick building systems in the farther reaches of space someday.
Butadiene—specifically butadiene 1,3—is one of the products of petroleum pyrolysis, or thermal decomposition, though it can also be produced from grain alcohol and acetylene and is a byproduct of ethylene production. First identified in 1886, butadiene was polymerized in 1910 by a Russian chemist. The resulting rubberlike material meant that the world now had a source of synthetic rubber, which came into high demand with the onset of World War II.
Styrene is a naturally occurring hydrocarbon that was first isolated in the early 19th century from the resin of a flowering shrub. Liquid in its native state, it was polymerized to produce a solid form in 1839, but when exposed to air, water, or heat, it can polymerize all by itself, turning hard with a slightly rubbery quality. Styrene was first industrially produced in the 1930s, and there are now multiple methods for producing it from ethylbenzene.
Sharp and glossy: the properties of ABS
When those three are emulsified, you get the properties that have made ABS the material of choice not only for LEGO bricks but for thousands of other products. Styrene contributes the distinctive hard, glossy surface. ABS has a relatively low melting point, but as a thermoplastic, it won’t burn. It has exceptional impact, chemical, water, and ultraviolet resistance.
As a manufacturing material, ABS is almost always opaque and can take on deep, saturated colors. It is easy to machine and can be injection-molded or extruded. The finished products are easy to paint and glue and can even be metal plated with copper or chrome. Chrome-plated fidget spinner? Elaborate fake nails? ABS is there.
Other than those things that millions of parents have stepped on in the middle of the night, ABS is in all manner of common products, including the one probably at your fingertips right now—the computer keyboard. It is used in housing for household appliances, cameras, and computers; is a common material for 3D printing; and is the stuff of pipes and fittings as well as automotive interiors (not under the hood, though, as the melting point is too low).
ABS is not particularly cheap as a raw material, and this will no doubt be a factor when you’re deciding what type of material to use. But as you can see from the above list of common uses, ABS provides some distinct advantages. Consider it if you’re creating a new toy, household product, or electronic accessory.
ABS, Over and Over
Like other thermoplastics, ABS can be remelted and reused, meaning it is actually 100 percent recyclable. That said, rare is the municipal recycling facility that can sort and chip discarded ABS (for reference, it is labeled 7 under the international plastics-type coding system). Although end users might have to do some research to figure out how to keep it out of the landfill, as a product maker, you have several supplier options for recycled ABS as a raw material—just ask your friendly neighborhood injection-molding company.
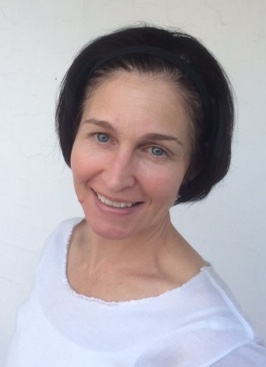
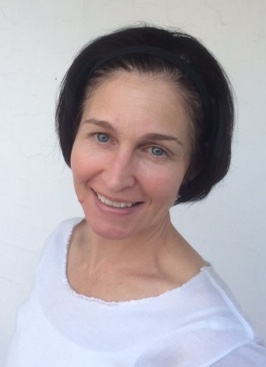
Jenifer Wolfe
Consulting Editor
Jennifer Wolfe has a curious mind and a gift for words and languages—if she does say so herself. A trained metalsmith and lifelong craft nerd, she loves handmade stuff, whimsical clothes, and traveling. A resident of Mexico, she is certain that tacos are the food of the gods.